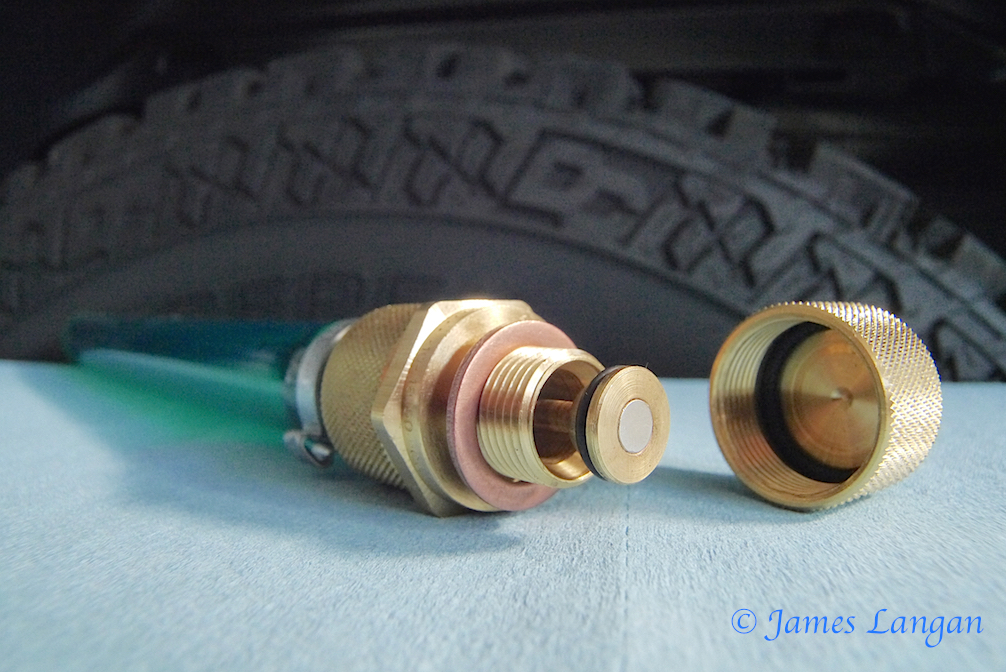
No-Spill Systems
Nearly two decades ago I learned about the No-Spill™ Systems oil-drain plugs from Geno’s Garage and have been a fan since. I love their quality and how they function. No-Spill’s housing and working parts are made with high-quality brass instead of steel. Some competitors use brass dust caps on steel plugs, and when the metals expand and contract at different rates the caps can fall off. No-Spill uses all brass construction, so the dust cap is more likely to get tighter as the parts heat-up, not looser. The brass construction is also intentionally sacrificial. Brass is softer than the steel of most oil pans, and if over tightened the plug will break or the threads may strip before those inside the pan. This is extremely important on large equipment and aircraft, where oil pans can cost thousands of dollars, plus the labor to remove and replace them.
In applications where a new washer/gasket is supplied, they are made from solid copper, not hollow core (fiber-filled) copper, and the spring inside the plug is stainless steel. The No-Spill was formerly manufactured in the Netherlands, but they now source all their metals from the United States with the final machining and assembly done in Canada.
Quality is the name of the game here, and often you get what you pay for. As a fan of top quality parts, I would rather buy the best, most-functional accessories whenever possible. All No-Spill Systems come with a lifetime warranty on all parts and workmanship.
The compact system on my 1996 7.3L Power Stroke F-350 sold to a buddy in 2014, was in-use for 18 years. Our Toyotas also sport No-Spills; one is a nine-year-old compact and the other a right-angle design. Using these has been a pleasure, and I can’t abide returning to a standard, messy oil changing process.
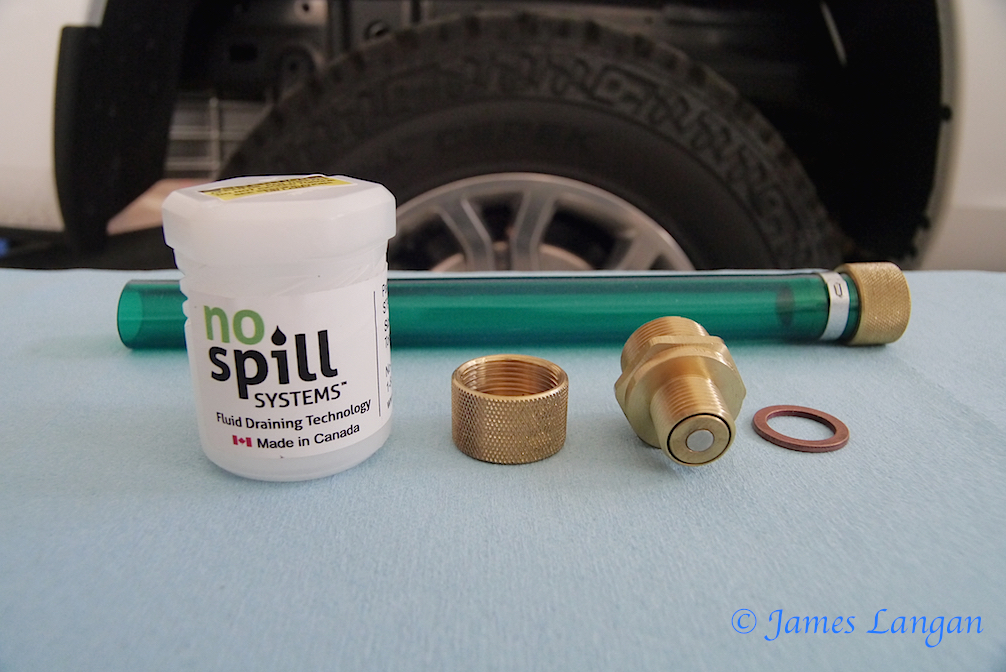
Magnetic
For our 2014 Ram/Cummins 2500 I chose a 10-18150-06, a standard design (not compact) with a magnet in the center. There are those that might argue that a magnetic plug is unnecessary with modern filtration, and if needed, Ram or Cummins would include one. Maybe so, and countless Cummins Turbo Diesels survive without one, but pulling the copy of Robert Sikorsky’s Drive It Forever from our bookcase, and reading his recommendations encouraging using one, the wisdom of my decision was supported by a higher authority.
A magnet and a real copper gasket were noticeably missing on the factory stopper I removed. Maybe the thin rubber film on the OE plug base would seal for many changes, but it appears cheap. Kudos to Ram/Cummins for only requiring a simple 3/8-inch ratchet for removal and for the low profile, high-clearance design.
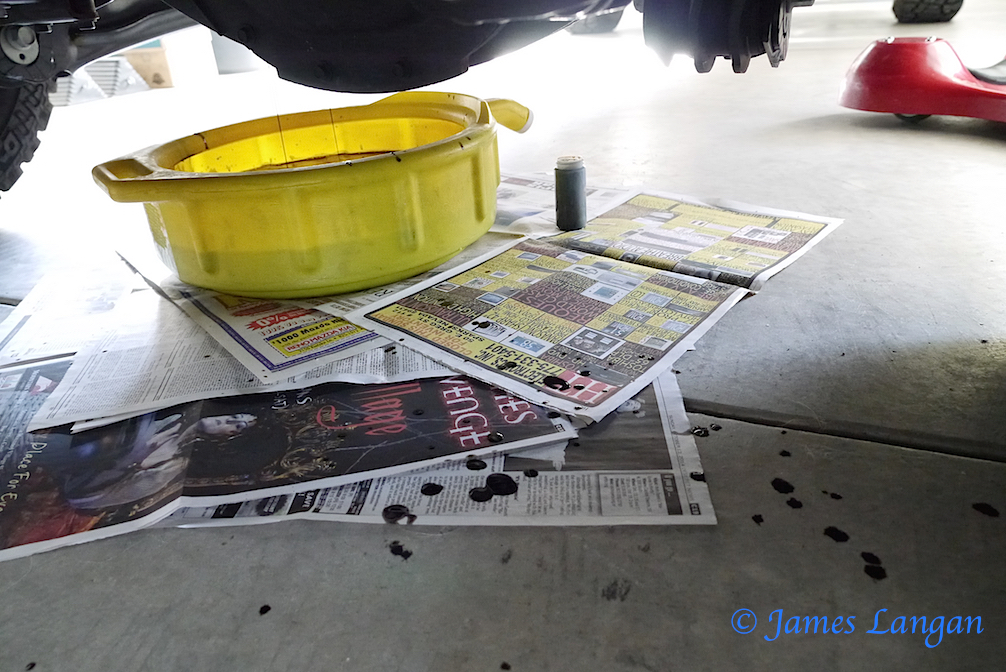
This No-Spill extends 1.2-inches below the bottom of the pan, not much, but being accustomed to the shorter compact design, it looks substantially lower. As a frequent backcountry traveler, I may change to a Compact, particularly if I don’t fashion a skid plate to protect the oil pan. It would take a large rock tumbling under the front axle to hit and damage this plug, but plenty of rocks have rolled under the soft white underbelly of my rigs during technical sections of trail. The consequences could be severe.
Installing the magnetic No-Spill was easy; with the one exception being it’s so large. Only because I’d recently purchased a 3/4-inch-drive socket set did I have the 1 3/16” socket I needed. Without a 3/4- to 1/2-inch reducer in my toolbox I couldn’t torque the plug to specification, instead I had to use old-fashion feel. After buying an adapter I confirmed it had at least 30 lb-ft of force applied. Subsequent changes will be a pleasure, devoid of splashing when three gallons of hot oil all fight to exit the pan at the same instant.

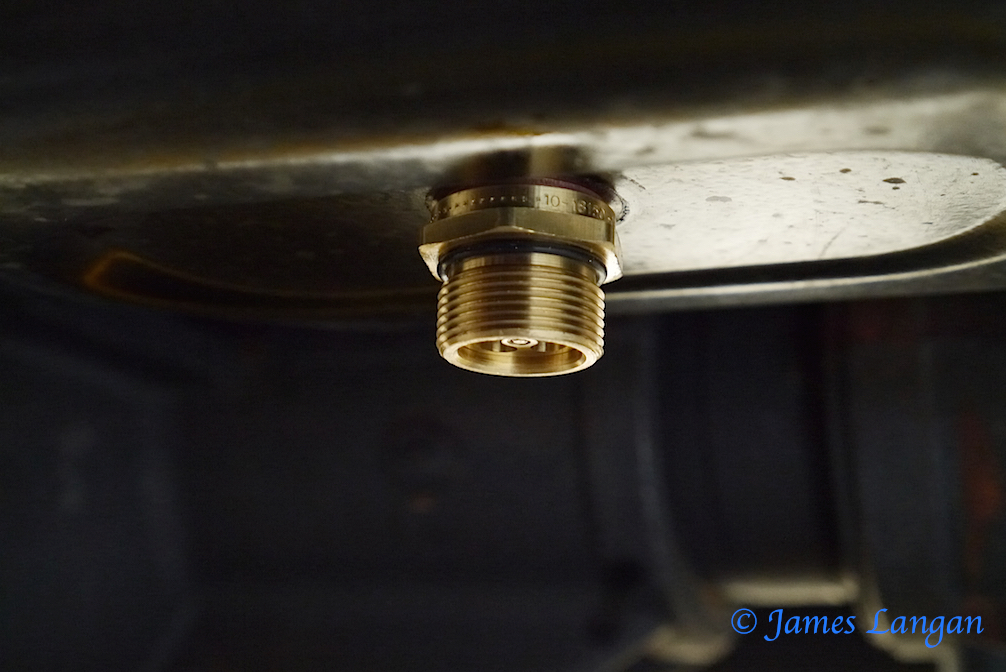
Oil Change Number One
This was the first new vehicle in decades that I avoided doing an extremely early, precautionary oil change, usually around 1,000 miles. When essentially new lubricant is drained from the latest generation Cummins ISB engines designed to travel up to 15,000 miles on fresh lube, it’s almost unused.
Modern engines are made to tighter tolerances, and there is less physical wear-in than in the distant past, but there is still some. The Ram owner’s manual speaks to this, saying “engine run-in is enhanced by loaded operating conditions which allow the engine parts to achieve final finish and fit during the first 6,000 miles.” Note the word loaded. Don’t be afraid to work a new engine. Use the whole rpm range and all the gears, plus transfer case (off-pavement) if you have one… stuff needs a “final finish”. Does this mean the oil should be changed before the EVIC says to do so, probably not? But learning that our maintenance regime might be overkill is a good, first-world-problem to have.
Doing early oil changes has not always been about dumping the factory fill for more of the same, but often to insert a preferred synthetic at what was traditionally considered very low mileage. Confident my engines have received a good and varied initial break-in during the first 1,000 miles, my anecdotal evidence has been zero consumption, leakage, nor any oil-related problems from modern cars and trucks after adding synthetic after few miles. At 1,000 miles the wear-in process has just begun on heavy-duty diesels, and towing and hauling use ensues. However, early use of synthetic oil in new Ram/Cummins ISB engines is not a concern, they are delivered with 5W-40 synthetic in the pans.
Three-Pronged Oil-Change Goal
Changing the engine lube in the new 2014 truck at 2,800-miles was about a few things, none of which were related to serious concerns about it being worn-out. The goals were: installing the No-Spill, using my chosen product, doing a baseline used-oil-analysis, and practicing the procedure once while the truck was new, clean, and before it needed a service. The first three are simple, but there are tips and a story surrounding the last.
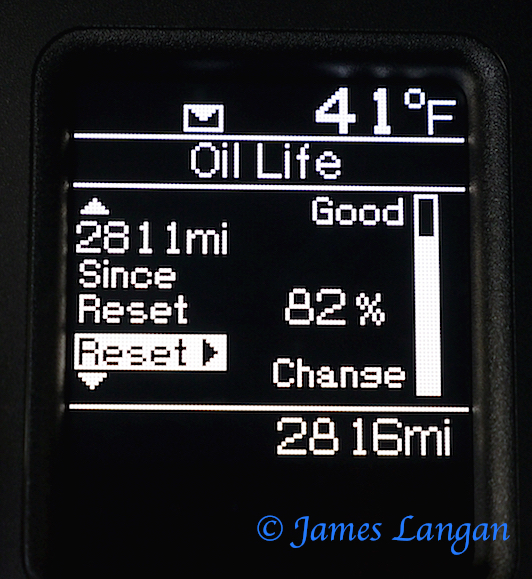
Changing engine oil is a simple task, but every vehicle is slightly different, and familiarity makes it easier and faster each time. Inline-six engines were historically straightforward to work on, our beloved Cummins ISB included, though like all modern vehicles there is increasingly little space under the hood and access is limited. Reading fourth-generation changing tips in both the TDR magazine and the Turbo Diesel Register online forums, I knew to remove the intake duct or use the passenger-side fender liner/wheel-well opening for filter access.
This 6-speed manual truck lacks the obstructive automatic transmission cooling lines near the wheel-well port. Access and leverage to remove the notoriously tight factory filter was much better through the wheel well, and there is no chance of debris falling into an open and exposed intake system. The fender-liner opening appeared faster and better.
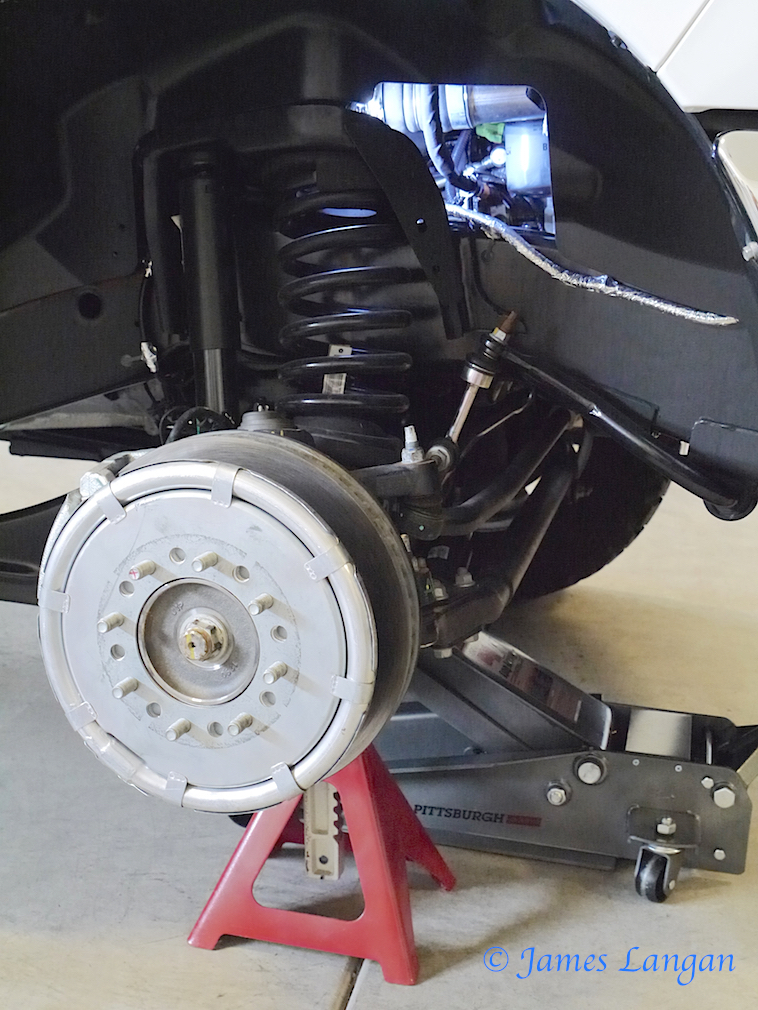
To make the job easier I removed the right front tire, a quick task because I frequently test different sets of tires and wheels and have-it-down. Lifting the front axle with a floor jack, lowering it onto a six-ton stand, removing the wheel nuts with a cordless impact gun, and pulling the tire took less than five minutes.
With the tire removed reaching the filter was easy, but a minor modification improved access. The block-heater cord was on the forward side of the battery ground cable to the block. It might have limited lowering a full filter, or caught my fingers, encouraging a fumble. Unclipping the cord from the ground cable and unscrewing it from the heater element allowed repositioning it to the rear of the battery cable. The reusable OE clip was attached, and I was ready to proceed.
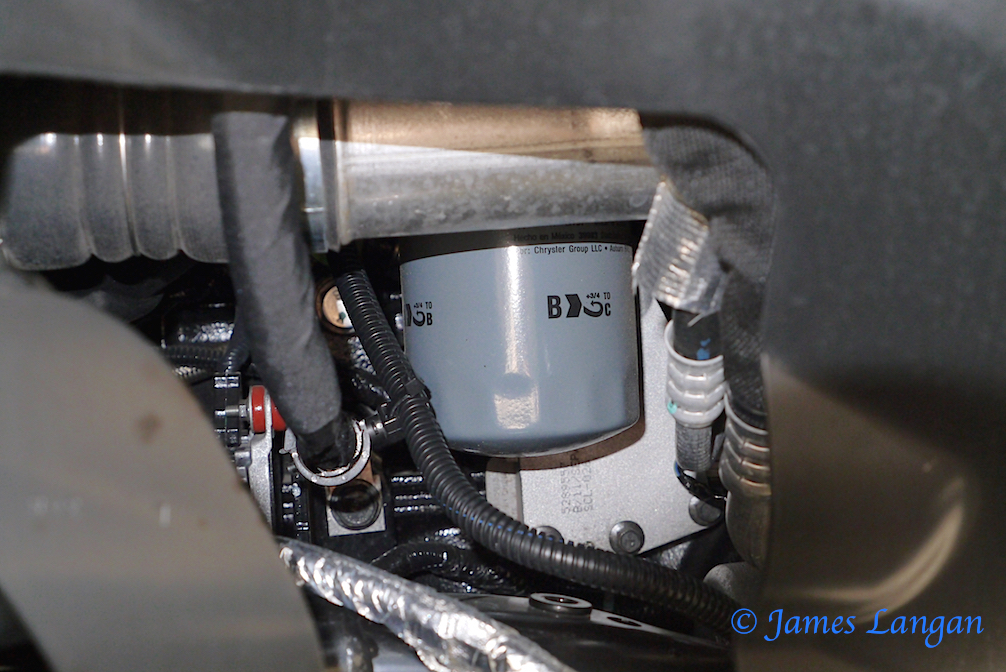
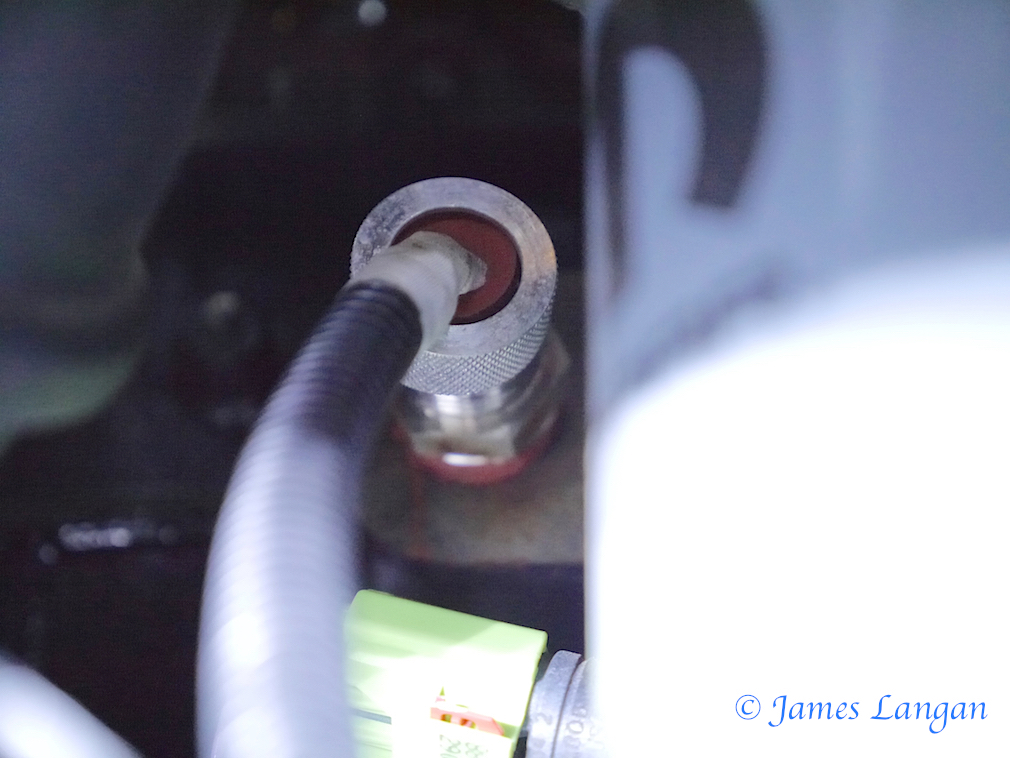
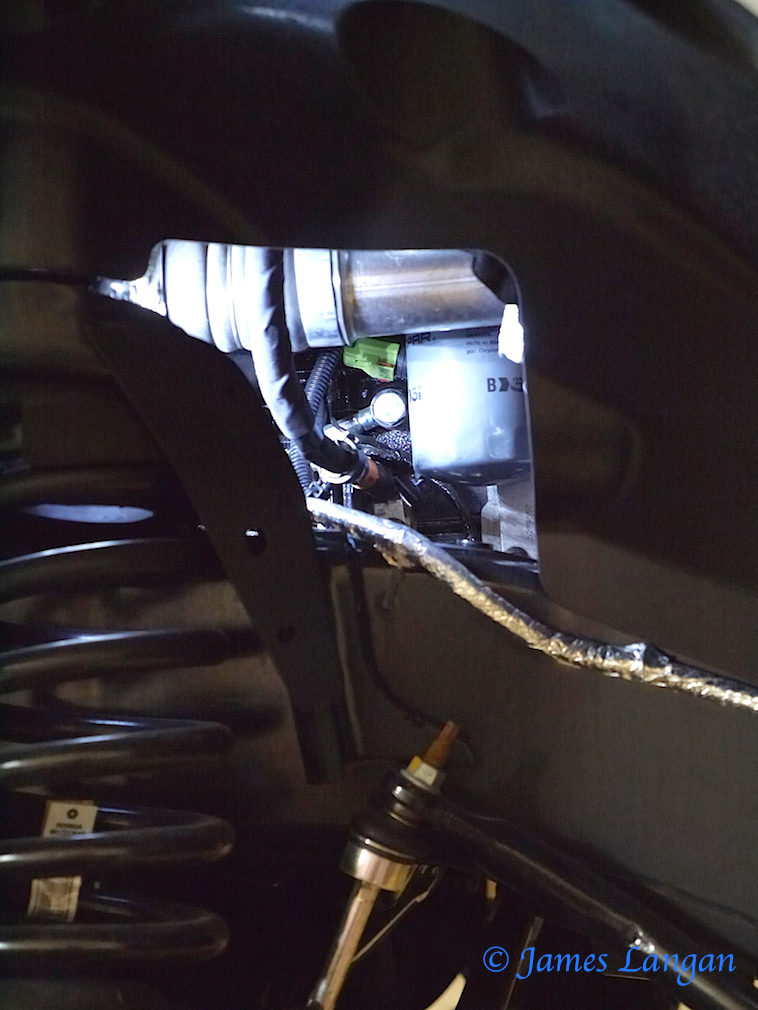
The metal band wrench purchased in 1993 for our first-generation Dodge Cummins Turbo Diesel still works perfectly. The filter was tight, I almost needed two hands, but I was able to loosen it without resorting to a cheater bar. After loosening, as a precaution, I used the gallon plastic bag trick. I’d read that the level would drop over time, and I’d eaten lunch between pulling the plug and returning to change the filter. Unsealing the filter resulted in zero spillage. Lowering the it into the space between the frame and engine, and then angling it toward me, I could see the oil level was about 1.5-inches below the top, and sealing the zip-lock bag was unnecessary. Pulling the filter through the liner opening allowed a few ounces to spill into the bag as I reached the maximum angle. The plastic bag technique provided a welcome safety net.
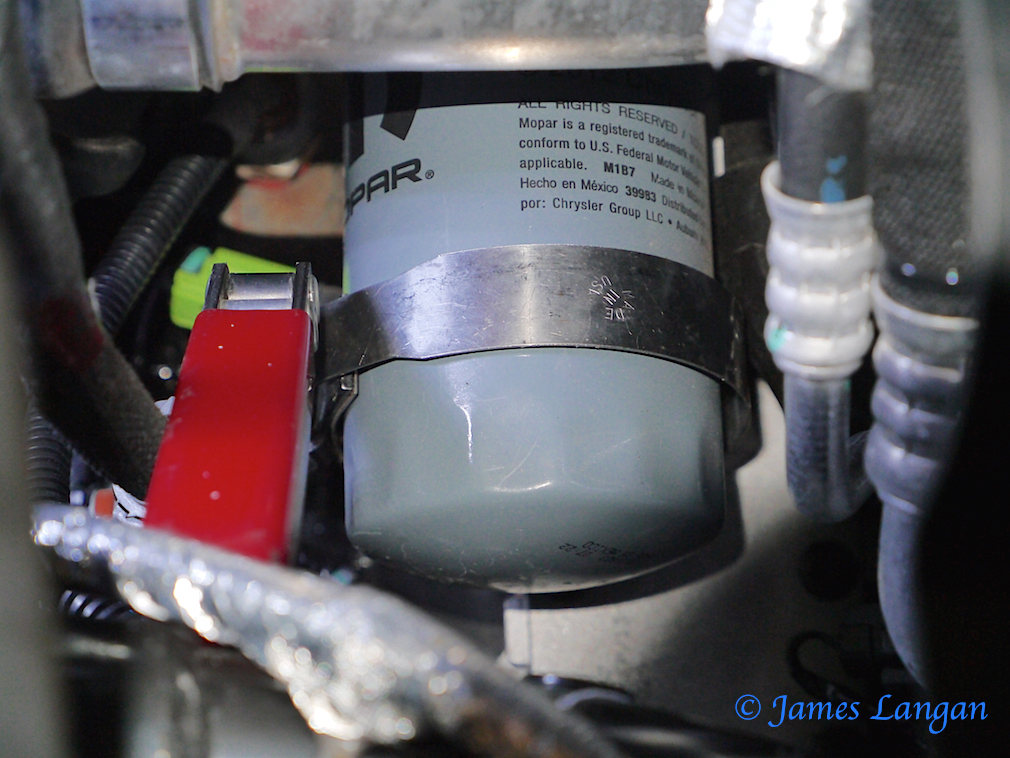
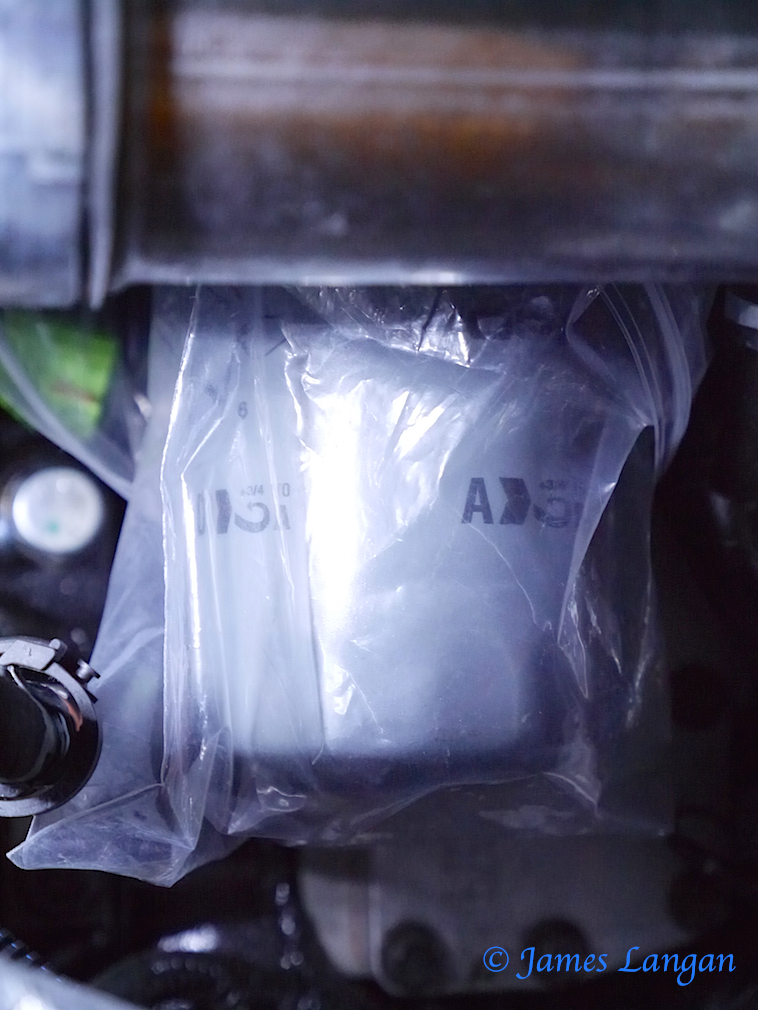
Filling new filters before installation has proponents and detractors. I’ve mostly been a filler, but the two Toyota V8s and VW TDI in our garage don’t allow pre-filling, so only the old ’96 Ford 7.3L (with superior access under the truck) has received this treatment in recent years. The Cummins Filtration Fleetguard LF16035 (purchased from Geno’s Garage) has pictures on the side suggesting filling before installation; I didn’t. Removing the risk of spillage or possible contamination, I was ready to add oil to the crankcase. It may sound like a small detail, but I appreciate the 12-quart capacity. Our ’96 F-350 7.3L needed 14 quarts, and it’s nice to just pour-in three gallons.
Aside from minor splashing after removing the factory drain plug, this was an extremely uneventful oil change with zero mess or spills—until I started pouring the last gallon into a funnel while looking through my camera viewfinder.
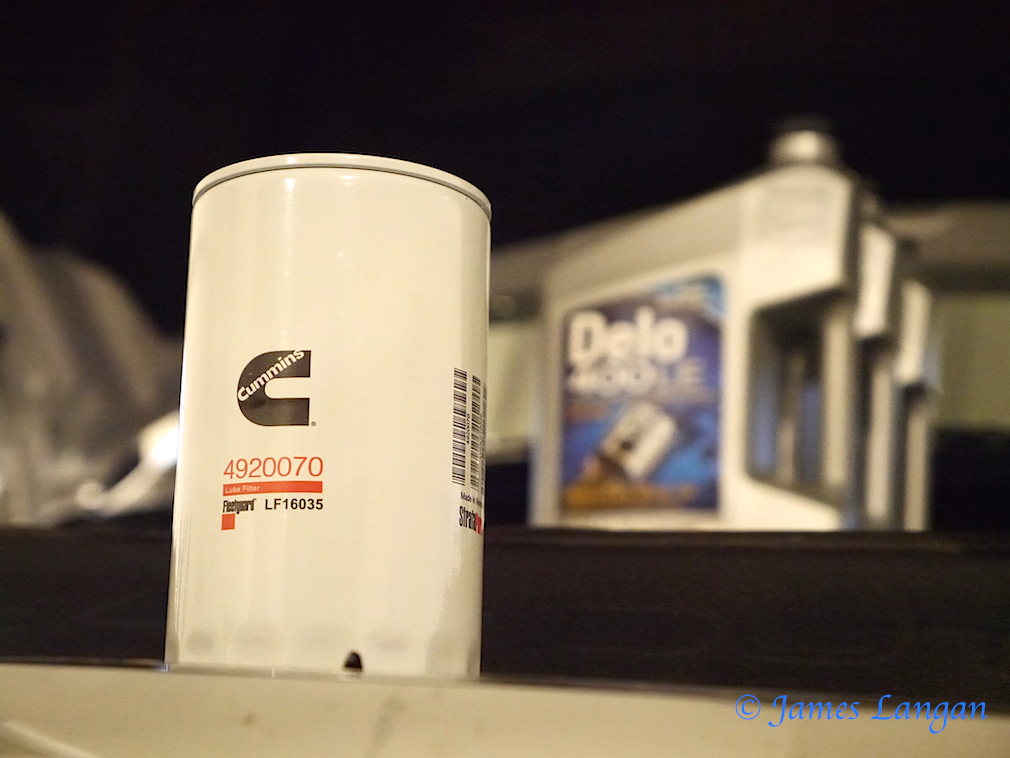
Oil Religion Conversion and Chevron Delo 400 5W-40
In recent years my preferences for some brands and products has evolved. I’ve read the Turbo Diesel Register articles about oils that “meet the specification”, and the difference or lack thereof between brands. I was a never an only this brand guy, but still I won’t buy the cheapest stuff I can find. Reputations matter, and I enjoy consistency. The Cummins ISB is tough, and I’m more concerned about the lubrication of other drivetrain components than the engine. There are many satisfactory lubricants; using one oil for a few applications simplifies things.
Several gallons of Delo 400 5W-40 already sat on shelves in my shop intended for other rigs when the new Ram joined the fleet. This Delo meets the specification, is readily available for a low price in my part of Nevada, and will suffice for all temperatures the truck will experience. This lube should work as well as any that meets the spec, and for fun and edification I send samples to be analyzed so we can see how the performance compares to the EVIC oil-change indicator. Using the 15W-40 suggested for temps over zero Fahrenheit is an option, but the truck will see its coldest temperatures in the backcountry, with no power for the block heater. So for now I like 5W-40.
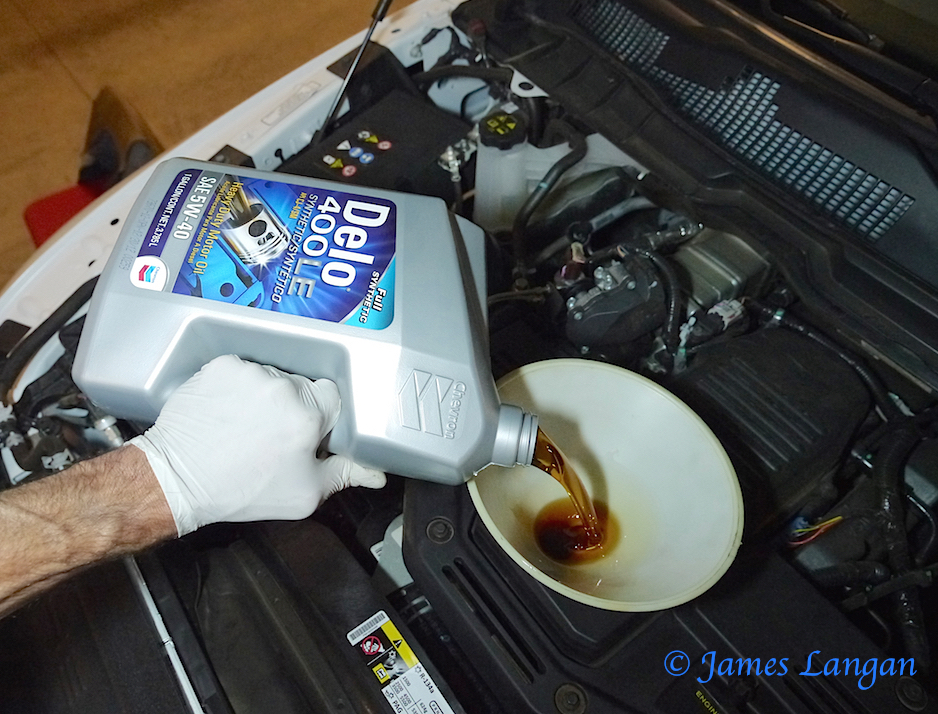
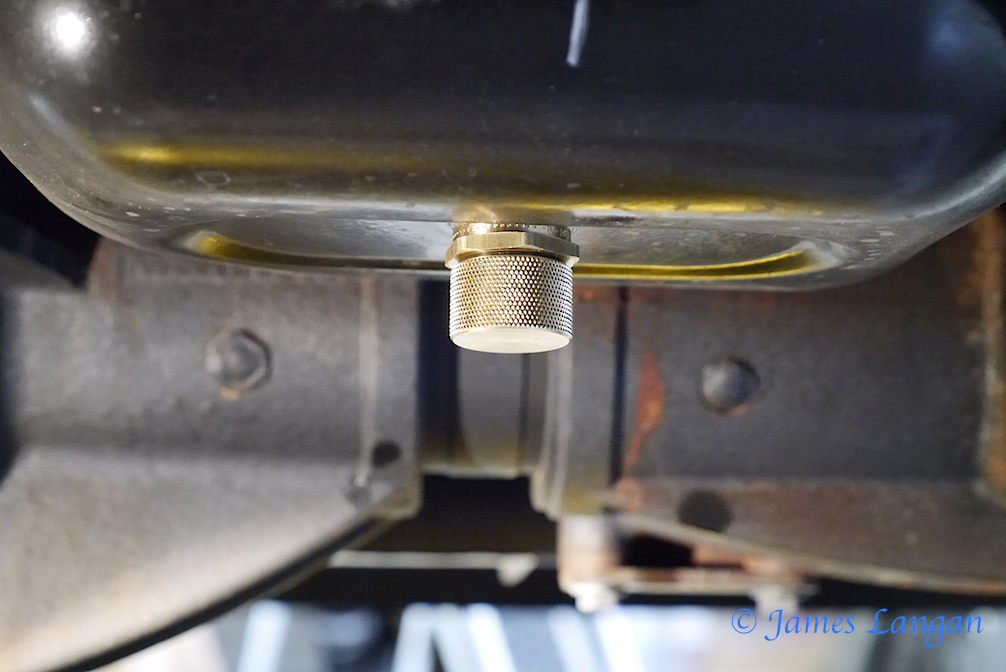
Future Change Intervals
The massive increase in oil-change intervals (OCI) on the 2013-up consumer pickups is due to the introduction of SCR/urea injection and the lack of oil dilution. I prefer a longer OCI when possible, and would not be wild about the shorter OCI on the earlier fourth-generation pickups. TDR editor Patton has confidence in Ram’s algorithm to determine OCI, and my EVIC numbers and percentages seem to support driving almost 15,000 miles before a change would be required.
After logging 2,816 miles on the engine the EVIC indicated the oil life was 82-percent of new. Simple math tells me that service life was reduced 1-percent every 156 miles. If that duty-cycle continued, I could have traveled 15,600 miles before needing a change. Impressive! This rig had yet to haul heavy loads or pull trailers, and doing so can reduce the oil’s longevity. Interestingly, the fuel-filter life was almost the same, with 81-percent remaining. The EVIC logs the engine miles and hours, and used oil analysis will likely backup the EVIC data. But what about a time-based OCI?
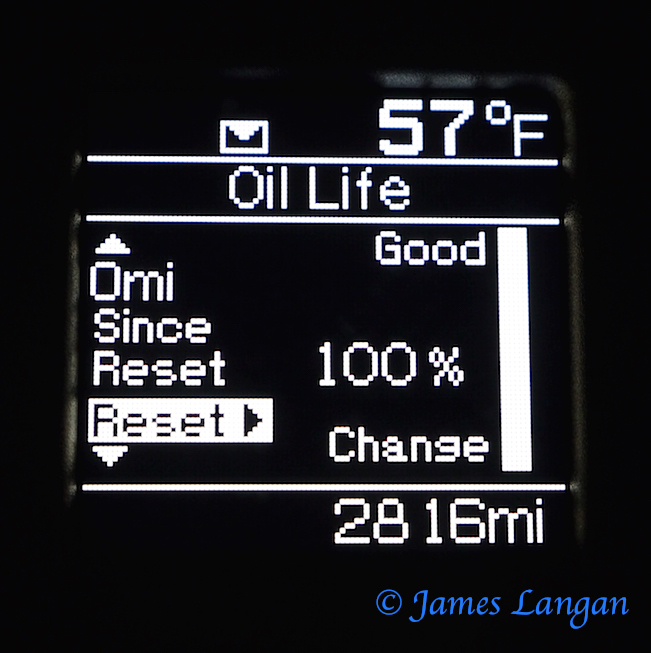
The 2014 Ram owner’s manual diesel supplement says, in bold, “replace the engine oil and oil filter every 15,000 miles (24 000 km) or six months, or sooner if prompted by the oil change indicator system. Under no circumstances should oil change intervals exceed 15,000 miles (24 000 km) or six months, whichever comes first.”
The six-month interval is ridiculously short. I’m calling bull on Ram and Cummins here. My truck was more than six month old when purchased. The lubricant was not changed before it was sent to me, the factory filter was still in-place, and the drain plug had not been touched. Was Dave Smith Motors in violation and my warranty in jeopardy because the engine lube was not changed? Did they sell me a truck that had not been maintained properly? Do the rules apply to me but not them? Balderdash. I’m confident the information obtained from oil analysis will show that about once a year will be often enough for a time-based interval. Avoiding draining three gallons of serviceable oil every six months will more than cover the cost of the oil analysis. We shall see.
Resources:
Geno’s Garage: genosgarage.com, 800-755-1715
No-Spill Systems: nospillsystems.com, 866-466-7745
© James Langan/RoadTraveler.net All rights reserved.
A version of this article was previously published in Issue 87 of the Turbo Diesel Register (TDR) magazine.